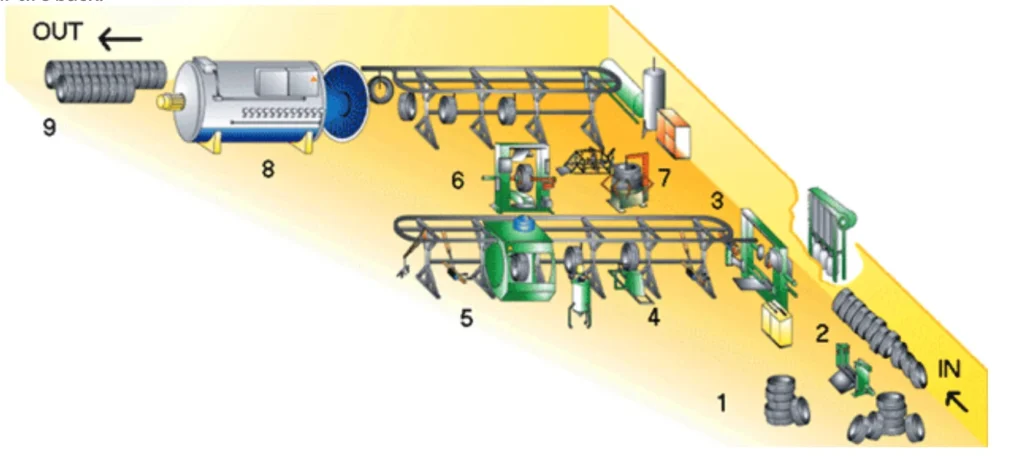
Retreading Process
Retreading is a process through which we can use our old tires. In this method, the worn cover of a tire which has a good structural property is unloaded and placed through a process in which it is completely refurbished and holds the rubber sideways. After that, the modified tire is pushed forward for an improvement process, in which the new rubber is vulcanized into the original cover and, therefore, the tire gets a new fabricated trade pattern. Over the years, there has been a lot of development in the tire manufacturing industry worldwide. High standard tires are being manufactured using premium technologies, so that they can perform not only in their ‘first life’, but also in their second and third lives. So, along with this, the retread tire industry is also growing, as stronger tire coverings, enhanced re-manufacturing technology and higher quality rubber compounds are being used.
A retread tire starts its life as a tire malfunction. When you find out that the trader is down to 2-3mm or if it is already re-waistned, or if your tire has punctures and needs repair, it needs to be stretched. In these cases, you will need to take your tire to an experienced technician, who will examine and inspect the tire to see if it is in a recoil position. If the specialist finds it okay, you can go to get your tire back.
1. Collection of casings
Wern tires are collected to select the appropriate casings for the tire retread.
2. Initial inspection
Each tire received at a retread plant is subjected to rigorous visual inspection. Inspectors are assisted by the use of non-destructive sophisticated inspection equipment such as the 540/2 Spectra or Nevera inspection machine.
3. Buffering after inspection
The older tread of the tire has been mechanically removed on high-speed buffers. Today’s buffers are highly accurate and will remove the appropriate amount of rubber, turning the tire to a precisely specified diameter and radius. The collaboration with international leaders such as MATTEUZZI enables Navira to make computerized world-class equipment under license for Asia.
4. Segment repair and skiing
With advances in state-of-the-art repair materials and repair methods, many of these tires can be repaired regularly and in most cases worn while running the original. The repair station is where any surface injury is treated using effective materials and equipment for grinding and patching.
5. Cement and Filling
Even in minor injuries, it is important that the injury is cleaned and filled. If this is not done, severe corrosion, separation and steel cable loosening can be taken out of service. The injury should be inspected, and then cleaned with a carbide cutter. After the injury is reinforced, a vulcanizing rubber stem must be applied to “fill” the injury. This will create a permanent repair that maximizes tire life.
With Nevera’s designed and built spray booth, your cement operation can be executed in a clean, efficient and environmentally responsible manner.
6. Building rubber
In the pre-curing system, the tread rubber is already vulcanized with the new tread pattern design. Buffed tires require a thin layer of cushion gum to be wrapped around their crown area. The pre-cured rubber is then applied with the building machine. This is called the manufacturing process.
7.
A) envelope and rim mounting or
Manufactured tires are again fitted with envelopes and rims to prepare them for curing.
B) double envelope system
For envelopes, the tires are first fitted into an outer envelope on the envelope-mounting table, before the inner envelope is fitted into them. The covered tires are vacuumed again to prepare for curing. In modern plants their veils are flanked by monorail systems. With professional planning from the engineers at Nevera, you can be assured of workstations that are designed to maximize output and make workflow easier.
8. Treatment by Chamber
The tire is placed in a curing chamber and the pre-cured tread is followed by the tire through a vulcanizing process.
Our extensive engineering capabilities and experience enable us to shape the different preferences of our customers, creating steam heating, electric heating or building new for double heating systems, semi-automatic and automatic chambers.
Monorail and hook systems increase productivity by cutting the possibility of contamination and allow for faster loading and unloading of tires. This increases the safety and productivity of your work space.
9. Final Inspection and Painting
Retread tires have been subjected to final inspection. This inspection states that only tires that meet industry quality standards are allowed to leave the retread plant. All retired tires are encouraged to return along the pavement painted using a light coat of black tire paint.
1.Tyre Testing System
The Shearography Tire Test System has been developed for non-destructive testing of new tires in R&D and quality control, as well as for inspection of tire carcasses in the retreading industry. The technical basis of the system is the phase shearography system.
During the test cycle, a pressure difference (vacuum, for example 50 m) is generated in the vacuum chamber, causing distortion, which is caused by
Expansion of air pockets occurs in defective areas in the carcass of the tire. With the phase shirography technique – a holographic measurement method that detects physical deformation in the micron range – the defective areas can be clearly and reproducibly
2. Buffing Machine
The method of computer programming and operation of RAS 90-DC is very simple and does not require any special preparation
The computer will accept up to 1,000 programs to give any buffer profile to spread “hot” or “cold”
high productivity
low power consumption
Suitable for tires from 12 ″ to 24 suitable (including 18-22.5 tires) – minimum external tire dismeter 515 mm., Maximum 1250 mm.
3.Tyre Repair Station
Ideal for truck tire repair or inspection
Handles all passenger, light truck and truck tires
Tires built in lifters lead to work height
Optional track for monorail system
Lifting capacity: 250 kg
Lifting height: 750mm
Air supply: 8-10 times
4.Retrax Extruder Machine
5. Tire Building Machine
Suitable for purchase process and camel
Applicable for light truck and truck tire sizes from 15 ”to 12.00 – 24
Double selection of sewing pressure for cushion gum, liner and camelback
Rotation motor: 2 hp / 1.5 quid with fast / slow speed selection
Stitcher Motor: 2 HP / 1.5 Quad with fast / slow speed selection
Voltage: 415/3/50
Total amperage: 10 Amp (approx)
Air supply: 8 times
6. OTR Envelope Spreader
Convenient installation and removal of outer envelopes
Applicable for sizes of tires from 14.00 – 24 ”to 2400 R35
Motor power: 2 hp / 1.5 quad
Voltage: 415/3/50
Total amperage: 5 Amp (approx)
Air supply: 8 times
6.Rim Mounting Station
Tilting table handles truck tires easily
Designed to handle all 20 ″ and 22.5 all preacher rims. Other rim sizes may be specified.
Air powered
Pressure required: 8 bar
7. Ferlex chamber
With safety, quality and breakthrough technology, Ferralex autoclaves provide high quality and uniformity to your production. They can be manufactured in many different sizes and configurations, according to the characteristics of the customer and production versions.
Radial locking door: Easy, fast and light opening and closing movement to require no lever, piston or other maintenance generating mechanism. Radial system avoids friction with trim, and reduces wear
Encapsulated motor: Since the motor is installed externally encapsulated, it is operating at low temperatures, but under the same pressure; The motor does not require any mechanical seal, motor winch and fan belt, thus the autoclave fan is running more efficiently and at lower maintenance costs
Internal thermal insulation: Since the device body does not require heating, its operation time is short, and this process is accelerated, thus increasing output, and enabling larger power or vapor economy goes.
Electric control board: Set up with high quality components, it provides high reliability and easy replacement. The electrical control board subsequently provides precise control of vulcanization magnification, thus securing the repetition of conditions in all working cycles.
Kit EPS (Third Pressure): Introduces a positive pressure in the movable design, allowing it to set the casing more firmly. Envelopes extend life time, distribute connections evenly, and prevent connection distortion
Double heating (optional): The autoclave can be supplied with double heating means, and can be worked with electric resistance or steam heat exchangers
final inspection
8. High pressure testing Machine
Handles tires from 15 ″ to 22.5 Hand
Tire inflation predetermined at 2, 4 and 8 times (maximum) for better QC inspection
Attached as security by steel cage
The test cycle ended automatically to reduce supervision work
Light well within the cage for better visual inspection
Driving motor: 2Hp / 1.5 Kw with programmable fast / slow speed
Power: 110V / 3Ø / 60 Hz / 40 Amp
Air supply: 10 times
Leave a Reply